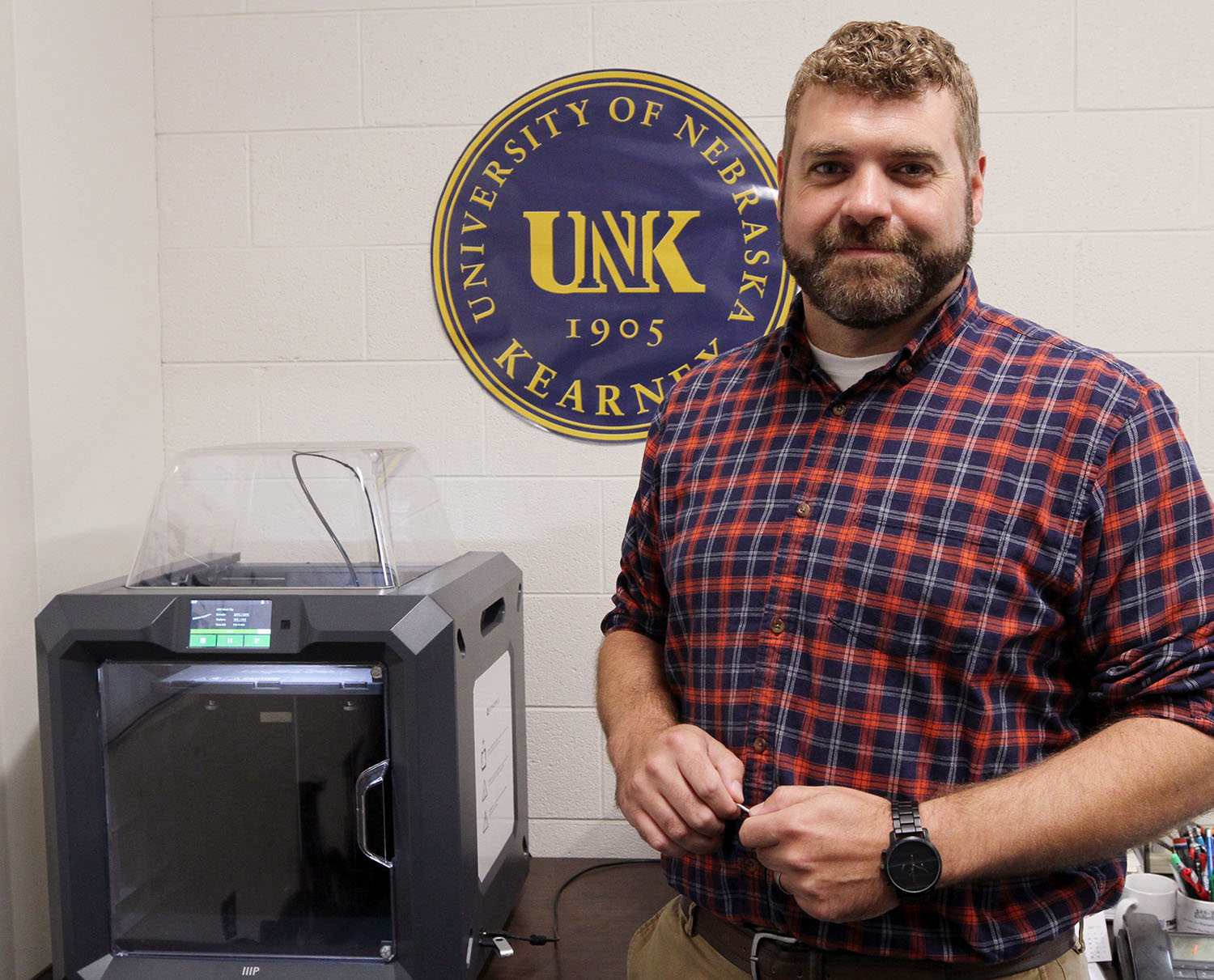
By TYLER ELLYSON
UNK Communications
KEARNEY – The project started with a worn-out plastic gear that’s part of the automatic door operators found across the University of Nebraska at Kearney campus.
This small component – about 3 1/2 inches in diameter – created a big problem for UNK Facilities Management and Planning when the manufacturer stopped selling the individual piece.
“In order to replace it, you had to replace the entire operator. That was $800 to $1,000 just for that one gear,” Michael Cremers said.
Cremers, the assistant director of UNK Facilities Management and Planning, had a better idea. Instead of wasting money on unnecessary expenses, why not make the part yourself?
That’s exactly what his department has been doing the past two-plus years.
UNK Facilities Management purchased a consumer-level 3D printer in late 2017, and Cremers started designing parts to meet the department’s needs.
As it turns out, that plastic gear could be produced in around 90 minutes using a 3D printer. The total cost – about $1.50.
“This part alone has already offset the cost of the initial printer, labor and materials involved in this program to date,” Cremers said.
Facilities Management now owns two 3D printers – one for production and another in Cremers’ office inside the General Services Building, where he develops prototypes using his background in computer-aided design software.
Cremers believes 3D printing can change the landscape of inventory management at UNK.
“We’re always trying to become more efficient in everything we do, and we can leverage technology to accomplish this,” he said.

MULTIPLE BENEFITS
By printing parts on demand, UNK Facilities Management eliminates obstacles such as discontinued products, minimum order requirements and shipping delays.
This process also allows the department to address unique situations, like when Cremers designed a small piece for a bathroom door latch. Using the custom design, technicians were able to solve a problem without adjusting the entire partition.
“The part took 15-20 minutes to print, and we didn’t have to tear apart half the room to make the repair,” Cremers said.
Of course, cost savings is another major benefit of the 3D-printing program.
Facilities Management currently produces about 10 different parts, many of which are around 90% cheaper than a standard replacement piece. For instance, the department makes light pole covers for less than $2 each, compared to an average cost of about $16, plus shipping, from a distributor.
“When we can print a part for $1 or $2 that normally costs us $15 to $20, that’s significant,” said Cremers, noting that the savings can be invested in other areas.
The program has an environmental impact, as well.
3D-printed parts can extend the life of products, reducing the amount of waste headed to the landfill, and less shipping means fewer transportation-related emissions. Energy use is also reduced when less warehouse space is needed.
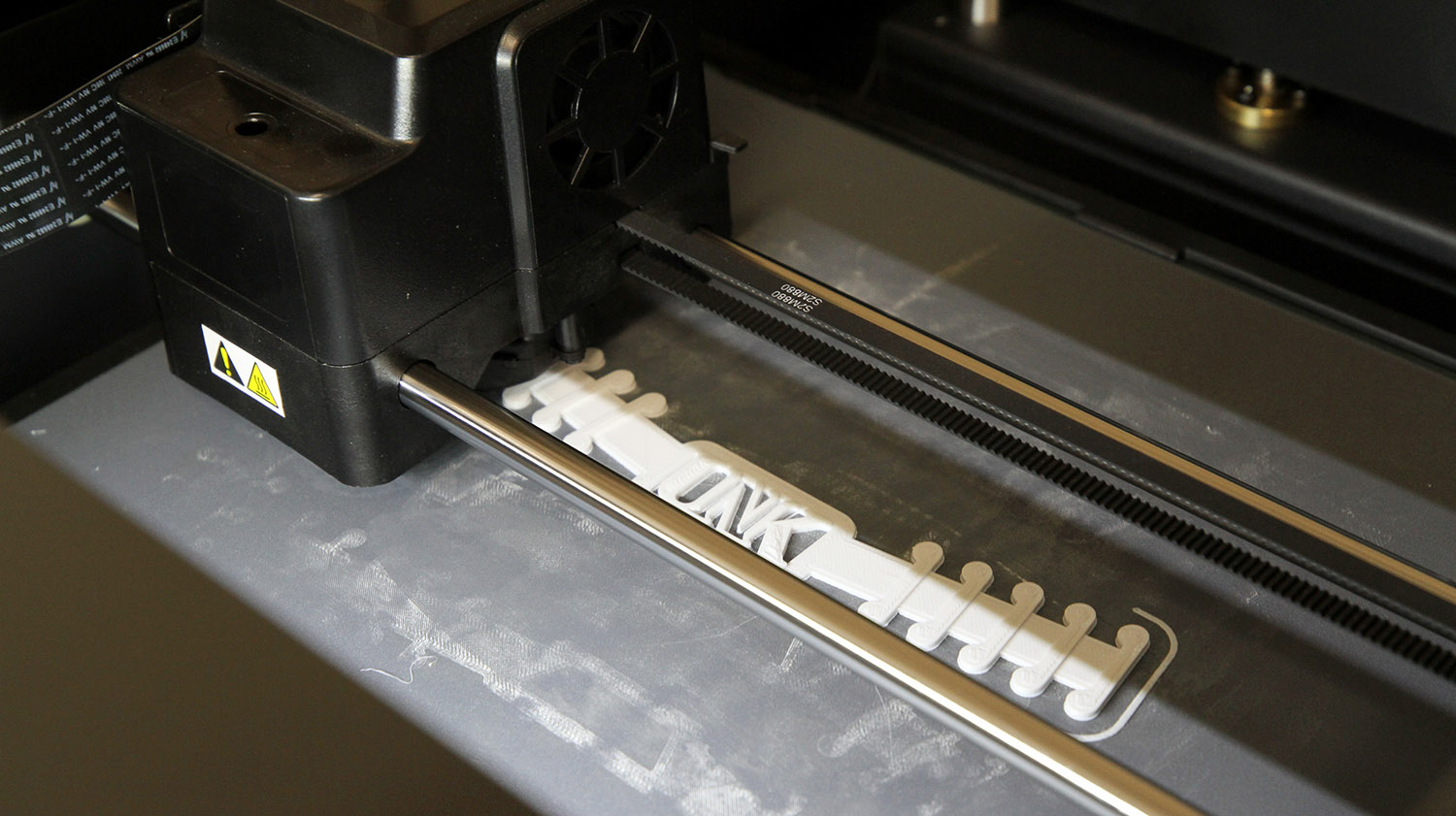
INDUSTRY AWARD
Cremers presented the 3D-printing program at a regional APPA convention last year in Winnipeg, Canada, and the industry organization recognized UNK Facilities Management this week with its Effective and Innovative Practices Award.
Previously known as the Association of Physical Plant Administrators, APPA represents more than 18,000 educational facilities professionals from over 1,300 institutions worldwide. Its Effective and Innovative Practices Award highlights cutting-edge programs that significantly benefit an institution and can be easily adopted at other campuses.
The 2020 recipients – UNK, University of Massachusetts Lowell, University of Virginia, Purdue University and Oklahoma State University – were recognized Monday during the APPA Virtual Facilities Summit and the honor will be announced in Facilities Manager magazine.
Moving forward, Cremers sees an opportunity to expand the program’s capabilities and provide real-world experiences for UNK students by partnering with academic programs on campus. He’s already met with several UNK faculty in areas such as art and design, supply chain management, industrial distribution, engineering and physics.
“The potential for academic collaboration is an exciting aspect of this program,” he said. “We believe both academic programs and Facilities Management would benefit from a joint effort on the planning, design, production and distribution of 3D-printed parts.”
Although the 3D-printing program is still in the “development phase,” Cremers knows the possibilities are nearly endless.
“Instead of a warehouse full of parts, I could see us having a digital warehouse of 3D models we just print on demand,” he said.